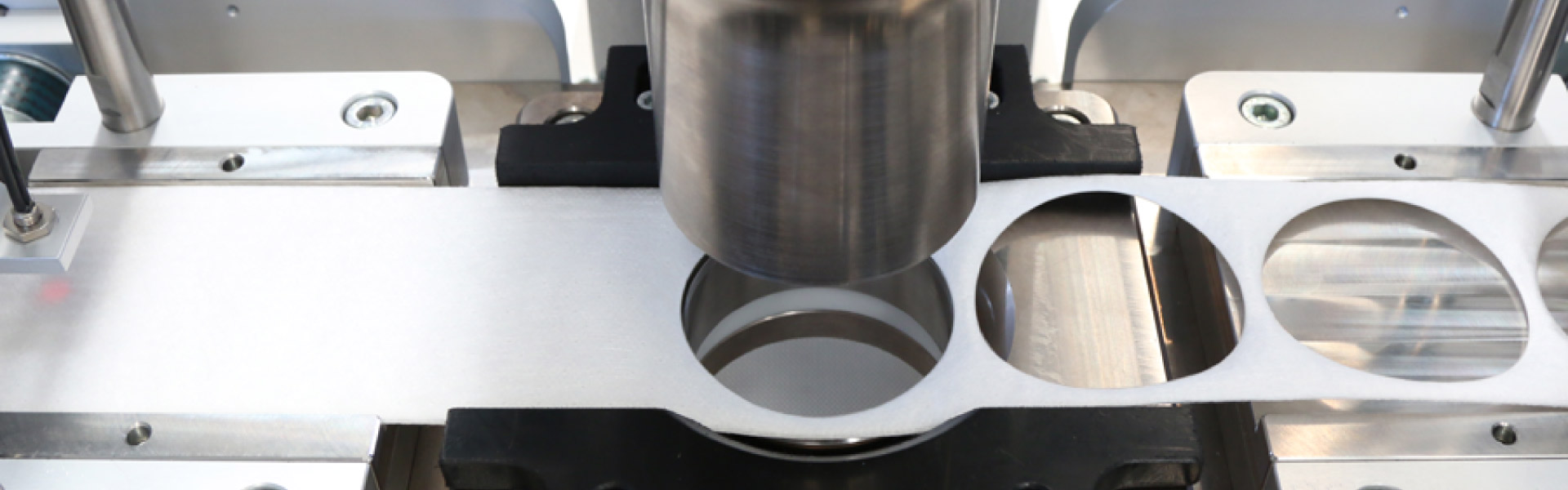
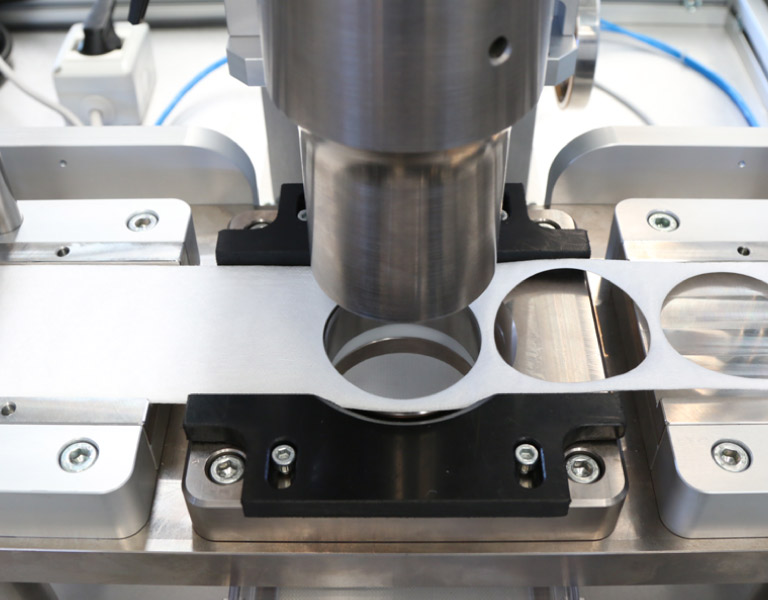
Plastic Welding Technologies
Sirius Electric, represented by EST in Mexico, manufactures and sells ultrasonic welders, hot plate welders, vibration welders, and spin welders. The various technologies used in the field of welding allow us to solve multiple challenges in assembling parts made from thermoplastic materials
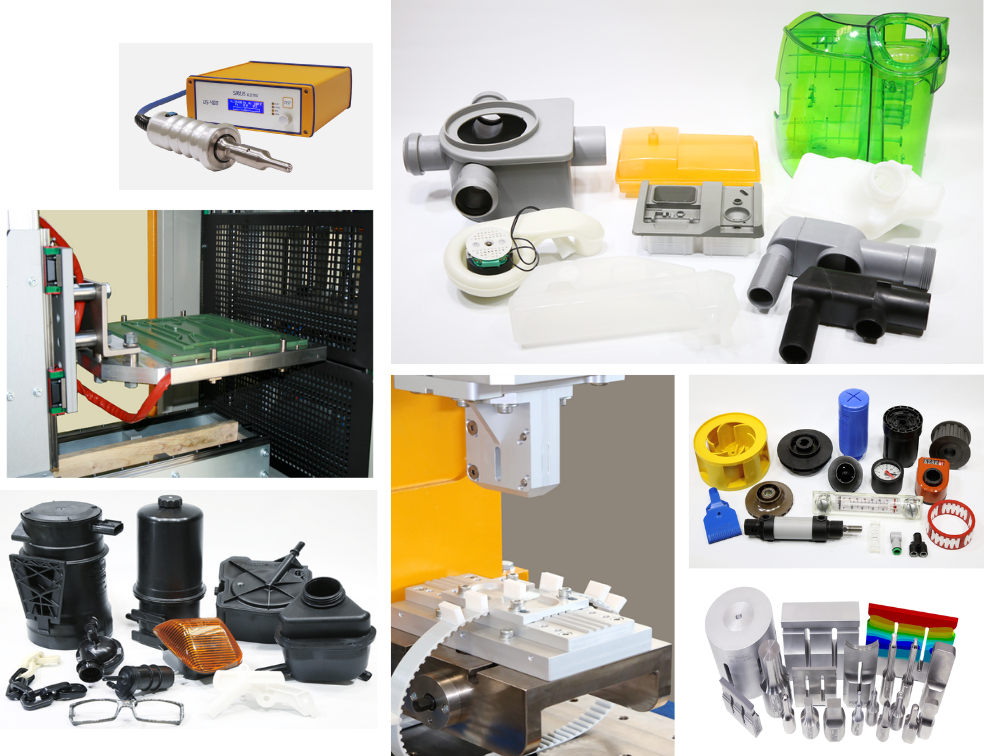
Request information
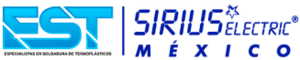
Quality
We manage the design process from the early stages, performing a detailed analysis of the welding joints and producing sonotrodes. All production is centralized, allowing us to supervise every phase and ensure exceptional quality.
Technical Support
We provide personalized technical assistance to resolve any issues or inquiries. Our team is always available to offer quick and effective solutions, ensuring proper operation of the welders, spare parts, and repairs.
Customization
In addition to our standard welders, we manufacture special machines tailored to customer requirements. For years, we have specialized in customizing machinery, meeting client requests with great expertise and the experience accumulated over more than 30 years in the industry
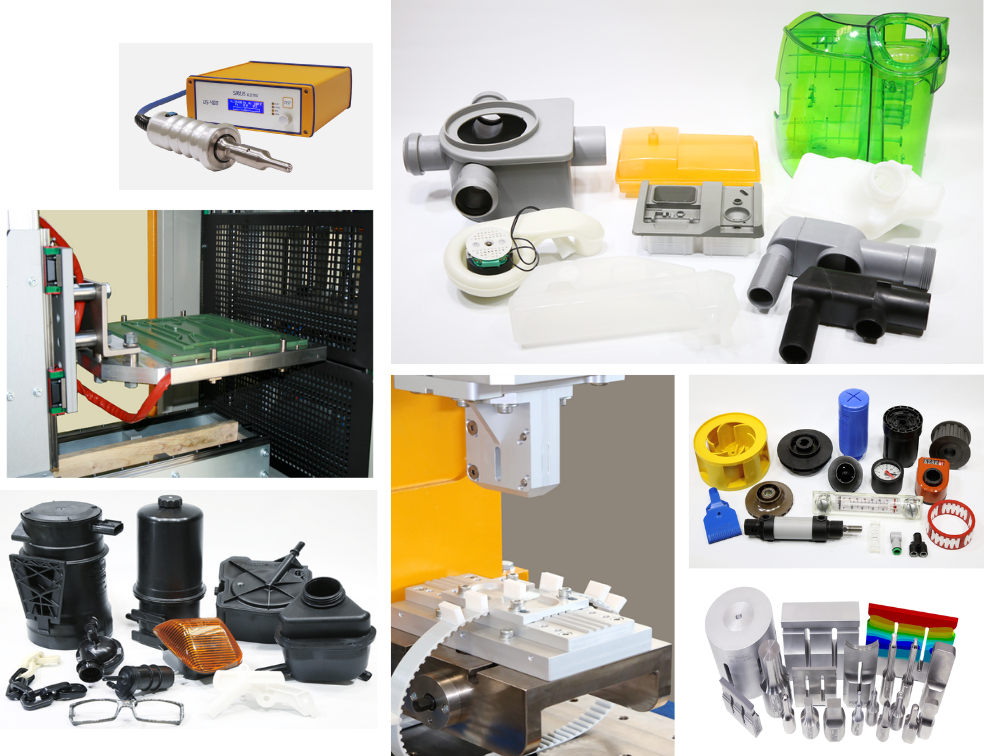
Request information
Products
Ultrasonic Welders
Applications of ultrasonic welding in plastic processing are diverse. The most common include welding technical articles, automotive components, household products, packaging, filters, or textiles. The devices vary depending on their specific use, but they all share components such as the ultrasonic generator, transducer, and a tool called a sonotrode.
-
Pneumatic Ultrasonic Welders
Pneumatic ultrasonic welders are designed and manufactured using the most modern technologies (3D CAD, CNC). The available mechanical and electrical solutions enable optimal working conditions and offer extensive adjustment options, adapting the welder to various welding challenges. The welder is managed by a next-generation microprocessor system, with straightforward and immediate programming.
Our range of pneumatic ultrasonic welders includes USP Energy, USP-M, USP APP, USP Dynamic, and many more.
-
Ultrasonic Generator US 400
Designed and manufactured for welding small thermoplastic parts. All calibration operations are available with a single control. Its ease of use, available features, and low cost make this generator unique in its category.
-
Sonotrodes and Accessories
The sonotrode generates friction between the parts through ultrasonic vibrations. This intense vibration produces heat, causing the thermoplastics to melt and ensuring the welding and assembly. Each sonotrode is designed considering all typical welding aspects. Materials such as aluminum, titanium, or hardened steel are chosen based on the application and cost. The sonotrode design is developed using computerized systems.
We also provide various accessories, such as soundproof booths or unwinding devices.
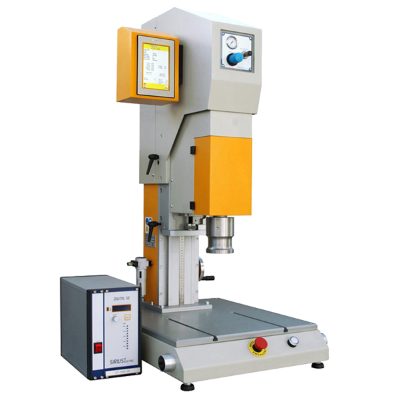
Vibration Welders
This technology is suitable for welding thermoplastics with complex shapes or materials with particular properties. In some cases, it is more advantageous than ultrasonic welding, such as in the production of technical items, filters, or conveyor belts. This technology is part of our production of machines for assembling plastic materials.
The joining of thermoplastics using vibration welding involves melting the contact surfaces. The necessary local temperature increase is achieved by rubbing one of the parts to be welded. A compressive force is applied to the moving part to maintain contact between the pieces during the welding process.
-
VSP 405 and VSP 416-L Vibration Welders
These welders are designed and built using the most modern technologies (3D CAD, CNC). This technology enables welding of thermoplastic parts with complex geometries or where the material itself is not weldable with conventional technologies (ultrasonics or hot plate). The VSP 405 vibrates circularly, while the VSP 416-L vibrates linearly.
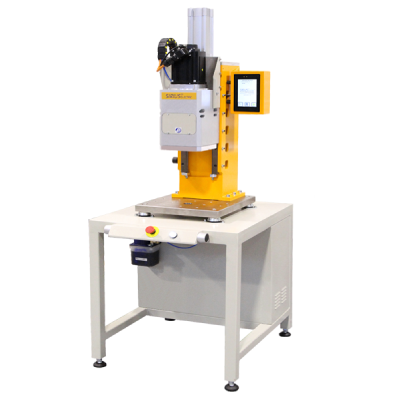
Hot Plate Welders
Hot plate welding involves melting thermoplastics through direct contact with an electronically heated and temperature-controlled plate (250–350 °C). Key parameters include applied pressure, appropriate temperature, and heating and cooling times. The parts to be joined are correctly positioned, and rapid mechanical movements ensure the joint is sufficiently pliable to achieve interpenetration of the parts.
Common applications include siphons, liquid containers, and technical articles.
-
Hot Plate Welder BASIC
Suitable for welding small to medium-sized thermoplastic parts, especially where equipment costs must be carefully considered. The BASIC series hot plate welder stands out for its simple design, reliability, robustness, and low cost.
-
Hot Plate Welder LINEAR
Designed and manufactured with the most modern technologies, it excels in quality and high productivity. The available mechanical and electrical solutions enable optimal working conditions with extensive adjustment options, adapting the welder to various welding challenges.
-
Hot Plate Welder DYNAMIC
The DYNAMIC hot plate welder is ideal for applications where the speed and precision of movements determine the welding quality. It stands out for its simple design, reliability, and robustness. This welder features brushless motors for horizontal blade movement and the descent of the upper mold holder.
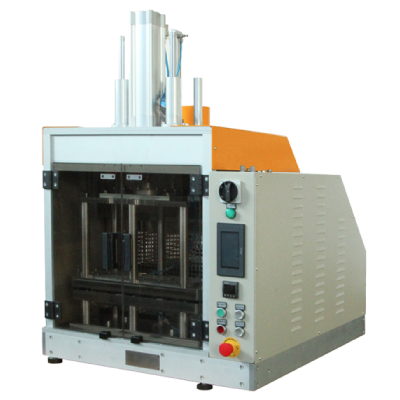
Spin Welders
This technology allows welding thermoplastic parts with exclusively circular shapes, such as water or fuel filters.
Thermoplastics are welded through spin welding by melting the contact surfaces. The necessary local temperature increase for the melting process is achieved by rubbing one of the parts to be welded. A compressive force is applied to the piece subjected to rotational movement to maintain contact during the process. In these spin welders, the rotation is performed by a precisely controlled motor, and a spindle is designed to match the shape of the part to be welded.
-
SWP06 Rotary Friction Welder
The welder’s structure is highly robust. The motor driving the rotary spindle is a brushless type. The motor head’s movement is pneumatic, managed by a proportional valve, and operates on high-precision prismatic guides. A key feature of this welder is its cycle control system, fully managed by a microprocessor.
-
MINI Actuator
For industrial automation in the assembly machinery market, we have designed and manufactured a new pneumatic actuator for rotary friction welding. This actuator, with very compact dimensions, is suitable for welding small parts where conventional systems are not practical due to size and high costs. The motor driving the rotary spindle is a high-efficiency brushless type.
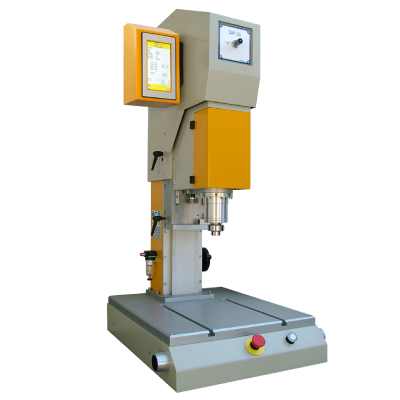
Special Welders
Keyword: Customization.
Defined as “special,” these machines are built, designed, and manufactured according to customer specifications. Customization stems from the ability to solve specific welding challenges. During the preliminary phase, the assistance provided to the customer includes guidance on designing the parts to be welded to improve their weldability. The electronic development department can adapt ultrasonic generators and cycle control systems according to customer needs. Finally, the mechanical design and production department manufactures special equipment: co-creation allows us to develop new and increasingly innovative systems. Through continuous technical support, even remotely, we assist the customer in case of failures or process improvements.
Examples include multitool welders for riveting or spot welding in the automotive sector, rotary table welders with integrated control systems, and additional stations that consolidate multiple manual steps. Sonotrodes can also be used with ultrasonic welders of different brands.
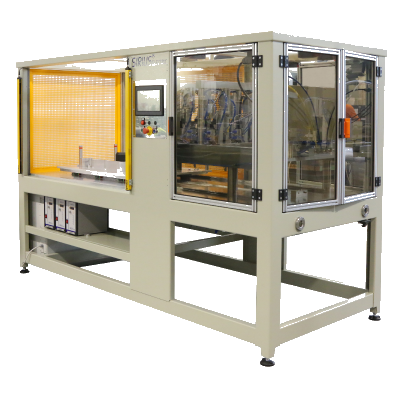
APPLICATIONS
We collaborate with numerous sectors where welding thermoplastic materials—simple and complex—is crucial for good mechanical strength of parts: from air or water filters to non-woven fabrics (NWF), medical components, and more.
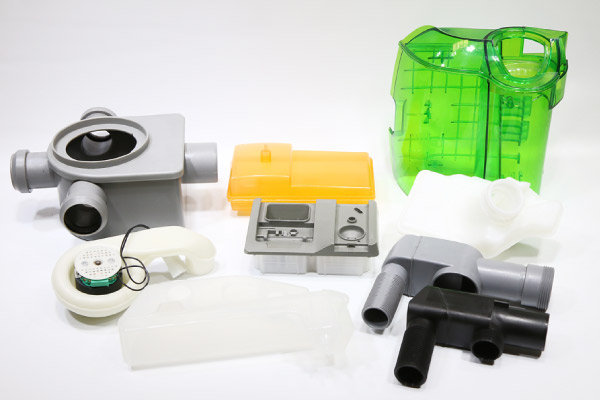
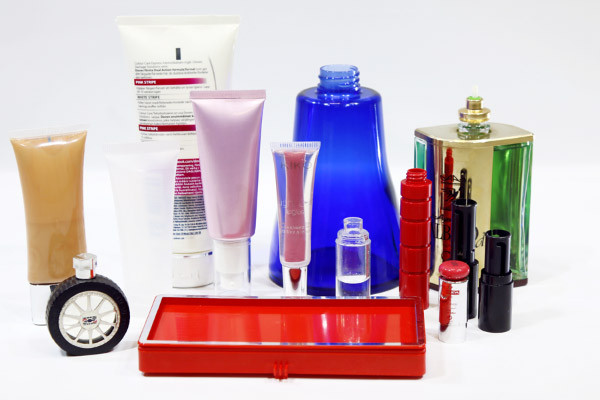
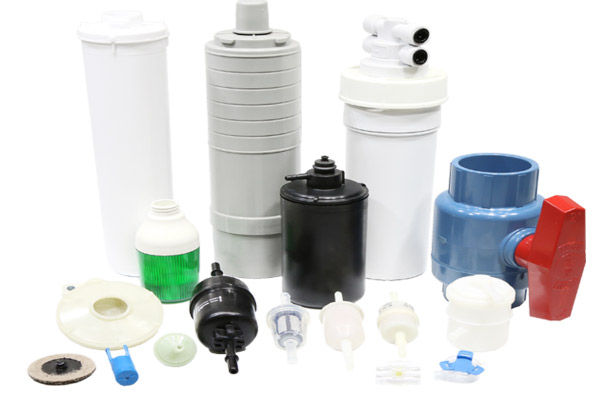
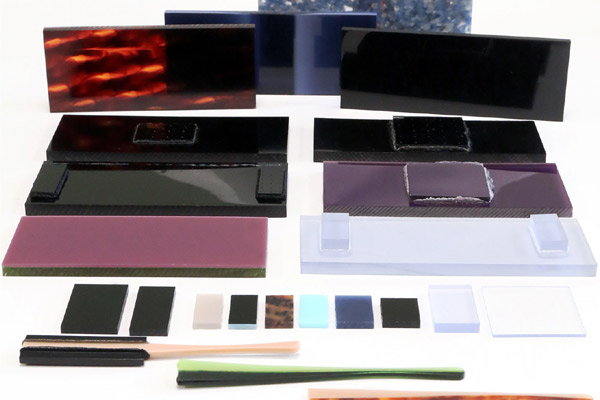
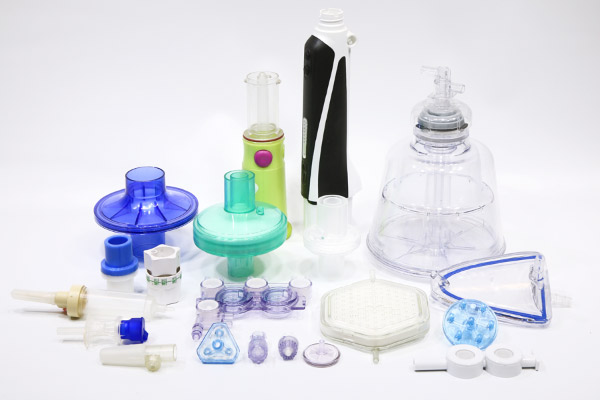
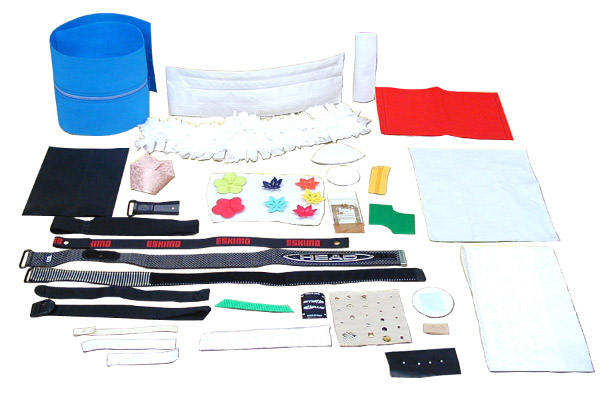
We provide solutions to any welding challenge.
Example? This hot plate welder with electric axes features two stations that can also operate independently, ideal for applications in the automotive, heating, and filtration sectors. The system includes a pre-heating process with infrared components before performing hot welding. Pre-heating is necessary to weld technical materials with significant glass loads, which would otherwise be difficult to weld.
Can we help you choose the technology that best suits your needs?